One of two reports surfacing from the UK this week. This is disturbing for 2 reasons.
1/ How did BHS not know that this factory may be of higher risk. Many factories where the management is not of the same nationality as the workers can, and do have problems with worker/supervisor relations.
2/ The requirement for suppliers to show they have a process for following the client's code of conduct would appear to be non existant.
Do you know what is happening in your supply chain? If you don't, this might be a report on one of your factories.
Get involved.
[Daily Mail] BHS knitwear is made by 'beaten and humiliated Bangladeshi sweatshop workers who are paid 10p an hour'
A high street chain is selling clothes made by sweatshop 'slaves' who are paid just 10p per hour, a report claims.
Workers making knitwear for Bhs are regularly beaten, threatened, stripped of their rights and imprisoned on false charges, according to workers' rights investigators.
The Philip Green-owned department store chain is among a string of brands who have items produced at the Chinese-owned Rosita and Megatex factories in the North Bengal region of Bangladesh.
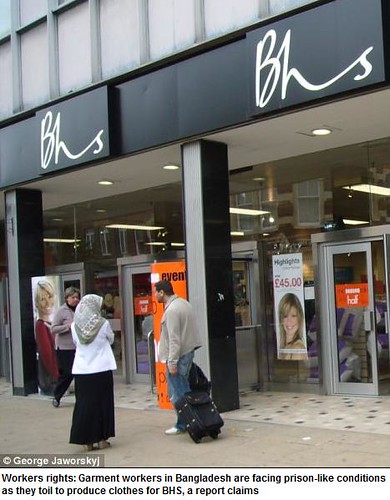
Investigators say that the factories' thousands of workers toil seven-day, 84-hour work weeks in conditions where every Bangladeshi labour law is routinely and systematically violated.
Now BHS, owned by billionaire fashion tycoon Sir Philip Green, has been called on to intervene.
The High Street giant, which sells its knitwear for between £15 and £35, boasts in its code of conduct: 'When customers buy our goods we want them to be confident that they have been produced under acceptable conditions.'
Last night a spokesman for BHS told The Sun the company was 'urgently' investigating with a supplier who had used the factories.
'It appears there have been a number of violations of our code,' the spokesman said.
Five thousand Bengali workers toil under Chinese management at the two factories, in conditions that a report by the Institute for Global Labour and Human Rights likens to a 'minimum security prison'.
During peak season - when overtime is mandatory - shifts last a gruelling 13 hours, from from 8am to 9pm, six days a week.
On Fridays, supposedly the workers' day off, there is a further six-hour shift from 7am to 1pm, meaning staff are routinely at the factory 84 hours a week.
According to the report, most knitters are on their feet for the entire duration of their shifts.
Corporal punishment is common at the factories, with workers who arrive late forced to stand to attention for at least for hours, without talking, turning their heads or even going to the bathroom.
In one shocking case, a woman who complained that a supervisor was pestering her for sex claimed she was then targeted for a savage beating by two other senior staff members.
Workers smuggled out labels to prove that they were making clothes for BHS and other major fashion companies worldwide.
BHS parent company Arcadia, which also owns Burton, Top Shop and Dorothy Perkins made profits of £190.4million last year.
The Bengali factory workers 10p pay means it would take 320 hours' labour to earn enough money for a £32 'multi-stitch' jumper from BHS's Olive and Olivia range.
Charles Kernaghan, director of the Institute for Global Labour and Human Rights, said: 'The Chinese-owned Rosita and Megatex plants routinely and systematically violate every labour law in Bangladesh as well as the International Labor Organization's core internationally recognised worker rights standards.
'Under Chinese management, the factories are operated like minimum security prisons. Under such circumstances, the workers are trapped.'
He added: 'The international labels must immediately intervene to end the gross violations and restore the rule of law.'